It has become clear that the role of supply chains on companies’ environmental impact is often very high. Up to a point, where 90% of your total environmental footprint can occur in said supply chains.
This impact percentage from your supply chain might seem impressive – but it also opens up many opportunities for substantial impact reduction.
This makes the role of procurement an important aspect in reducing your products’ impact.
- Are the products that I am shipping actually sustainable?
- Are the manufacturers of the materials/ ingredients I use in my production process sustainable?
- Should I have a better look at my key suppliers?
Step 1: Measure your supply chain’s baseline performance.
When it comes to measuring the environmental footprint (a Life Cycle Assessment or LCA) of a product or portfolio, a footprint can be split up into three categories (we follow the same categorisation for LCA footprint results as the GHG Protocol with GHG emissions):
- Scope 1: direct emissions from your own controlled sources;
- Scope 2: indirect emissions from purchased energy;
- Scope 3: all other indirect upstream and downstream emissions that are not owned/not directly controlled by your company.
Scope 3 emissions often account for the biggest contribution to your overall environmental impact (up to 90%). A big chunk coming from the supply chain of the company. So, although you do not directly own or control these emissions- they are highly connected to your company’s activities.
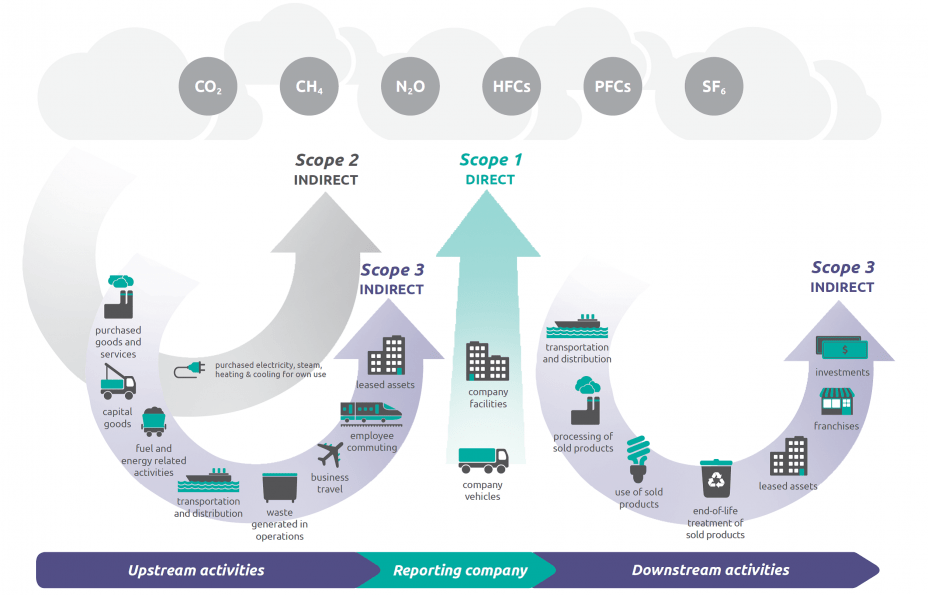
Measuring your first LCA
Before you start finding/engaging with sustainable suppliers- it’s advised to first map out all the processes in your supply chain and list your suppliers per step. This process is included in the data collection in measuring an LCA- it’s called a Life Cycle Inventory. Once you’ve done the mapping, you measure your product(s)’ complete footprint with a product or portfolio tool – which includes your supply chain’s baseline environmental performance (Check out our product footprint tools Mobius & Helix).
Usually, this first LCA calculation is based on already existing (average) environmental background data on supply chains. In LCA terms we call this ‘secondary data’. It allows you to make a first LCA with clear impact hotspots, without having to really dive into your raw supply chain data yet.
Having these initial hotspot results, ensures efficiency and transparency in knowing which suppliers to focus your efforts on. It prevents miscommunication and inefficient impact reduction efforts based on loose assumptions.
How do you interpret these hotspots?
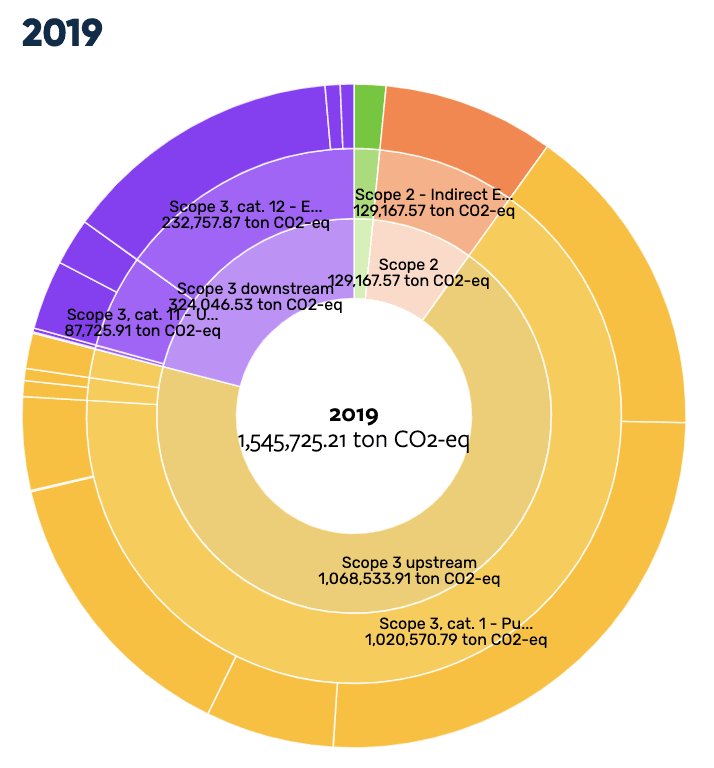
Step 2: Find the environmental hotspots in your supply chain and connect them to specific suppliers.
Once you mapped out your supply chain, you have an overview of the environmental impact per-process in your supply chain (image 2). Meaning, you can start looking for the environmental hotspots within your supply chain. Which process(es) accounts for the biggest impact? Could it be the raw materials for the production of your product?
You can connect your hotspot results to the suppliers within these processes. It’s often the case, that just a small number of suppliers can be responsible for the largest impact in your supply chain’s impact.
So, why is this the case? Is it their production processes, or are the core ingredients impact intensive? Time to start engaging with your ‘hotspots’ suppliers.
Requesting primary environmental data/product LCA’s from suppliers
We already now have an LCA based on averages (secondary data). But to make your own footprint measurement as accurate & credible as possible, you need to receive (as much as possible) raw data from suppliers too. This raw data is called ‘primary data’. You can ask for specific data you need on manufacturing processes, but requesting a product LCA from your suppliers is the most ideal situation. A product LCA gives you exactly all the information you need for your own measurements and helps suppliers to gain insights into their own footprint too.
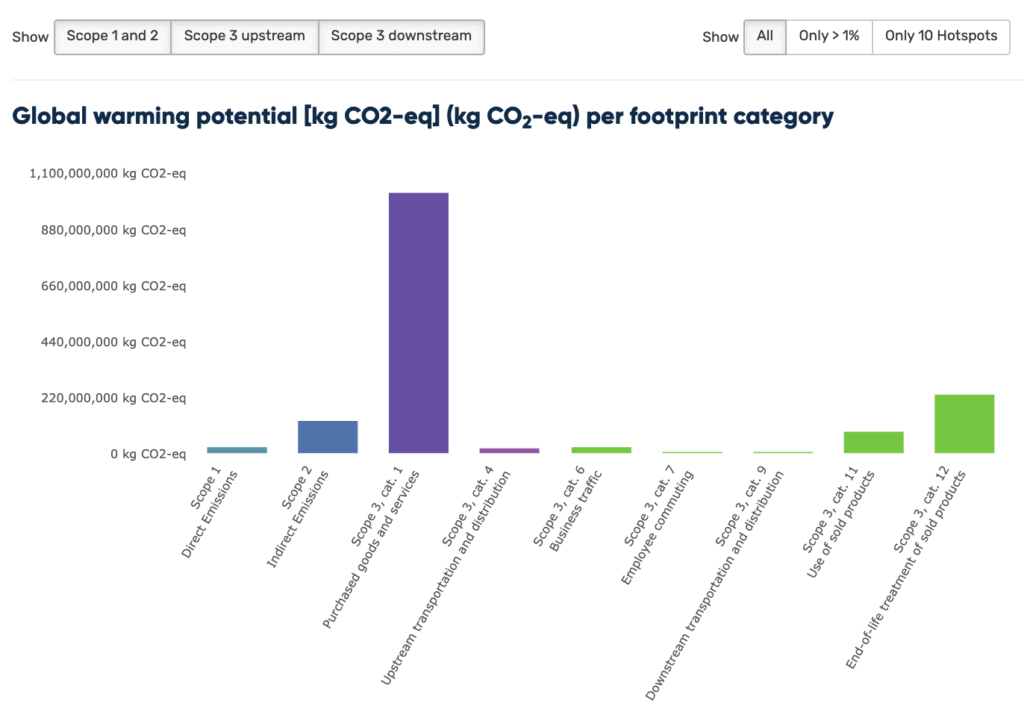
Step 3: Find opportunities to ‘creating shared value’ with suppliers and build a reduction strategy.
You now have the (initial) environmental data of your impact hotspots and know which suppliers account for said impact- the next step is to sit down with your suppliers and identify possible improvement opportunities for both of you. If you haven’t gathered primary data from your suppliers yet, this would be a good opportunity to do so.
The goal here is to create shared value. What could your suppliers do in order to become more sustainable, that benefits them as well? What are the business opportunities they can get out of collaborating with you and/or providing you with product LCA’s?
Read more about Harvard professor Michael Porter’s approach to creating ‘shared value’ in Business right here.
- Try to understand their position and stakes and search for ways to make supplier engagement more marketable for your suppliers. For example, you could challenge your suppliers to use more expensive renewable materials, and in return, you can offer them a long-term contract,
- Developing a long-term relationship with your key-suppliers, allows you to create strategic improvement scenarios and provides a backup that can help both of you succeed in this sustainable improvement process.
Different collaboration types with suppliers
There are multiple ways in which you can approach your suppliers. And the approach should fit the size of your company, your company’s culture and values, and your position in the supply chain. In the table below you can find the most common collaboration approaches described (Image 3).
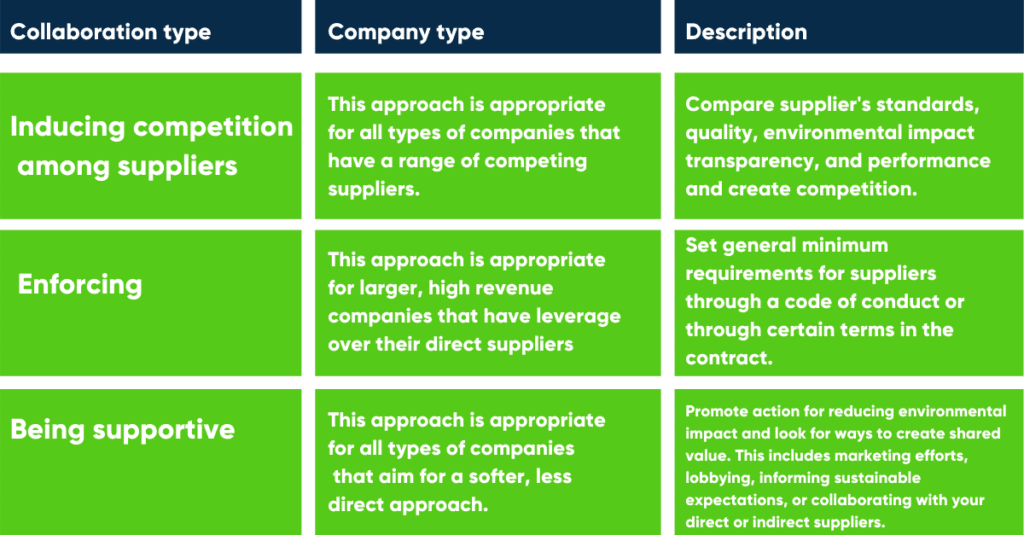
If you are searching for new suppliers, take a good look at your environmental data and set certain selection criteria for yourself. These criteria can be based on shared values and mission statements- which often form a solid base for developing joint projects or strong relationships.
You can also look for suppliers that offer similar products, but have credible information/ environmental data to prove their sustainability. For example, with non-critical suppliers (think of cleaning products) sourcing for alternative products is the easiest.
Step 4: Set sustainability or circularity targets in collaboration with suppliers
After you agree with your suppliers on a reduction strategy based on shared value, start setting up fitting sustainability key performance indicators (KPI’s). These targets will help you and your suppliers evaluate your progress and track supplier performance. Next, define a common baseline and decide on a policy should your baseline be adjusted. It’s crucial you understand the actions that with help you achieve these KPIs in order to be able to monitor them.
Step 5: Monitor the improvements throughout your supply chain
Once you have new or adapted suppliers as part of your supply chain- see if what you’re doing is actually working.
Always. Keep. Monitoring.
We advise you to set up your monitoring process by using your supply chain targets as the starting point. By continuously monitoring your upstream and downstream environmental impact (image 3), you can:
- Reflect if your environmental measures are effective or not. Indeed, through annual monitoring;
- Steer your sustainability strategy if needed and identify possible new opportunities for improvement.