Cradle-to-cradle or cradle to cradle, does not let old products go to waste. Instead, a product’s materials and components are repurposed or recycled. This keeps materials “in the economic loop” and saves energy during production. Win-win.
The “circular economy” received increasing international attention since 2010. Its main purpose: revolutionize how materials are used in our economy. This is where the model ‘cradle-to-cradle’ emerged as the ideal for products’ lifecycles.
Cradle-to-cradle is usually associated with the design principle and methodology created in 2001 by professor Michael Braungart and William McDonough. Its’s abbreviation C2C. This design approach is accompanied by a sustainability label for products that are C2C designed and certified. However, cradle-to-cradle is also applied in the scientific method Life Cycle Assessment (LCA). Which is what we discuss in this blog.
In this article you learn how cradle-to-cradle:
- relates to LCA;
- is incorporated into sustainable product design
- benefits your product’s LCA results;
What is cradle-to-cradle?
Cradle-to-cradle is one of the several “lifecycle models” that guide the scope and methodology of Life Cycle Assessments. Life Cycle Assessment (LCA) is THE scientific method to measure all environmental impacts of a product.
Lifecycle models in LCA
To dive into the cradle-to-cradle model, we first need to understand the lifecycle of a product. Just like people, products go through several “lifecycle stages”:
- Raw Material Extraction, also called the “cradle”
- Manufacturing & Processing
- Transportation
- Usage & Retail
- Waste Disposal, also called the “grave”
Based on the stages you’re interested in or have data available on, you can choose to leave in or take out phases when you measure the footprint of a product. Basically, you decide: how much of my product’s lifecycle do I want to measure the impact of?
There are 3 main product lifecycle models you can implement in LCA:
- Cradle-to-gate: Cradle-to-gate only assesses a product’s footprint until it leaves the factory gates before it is transported to the consumer (stages 1 &2).
- Gradle-to-grave: Cradle-to-grave includes all 5 life stages in your footprint measurements. It shows a full footprint from start to end.
- Cradle-to-cradle: Is a variation of cradle-to-grave, but exchanges the waste stage with a recycling/upcycling process that makes it reusable for another product – essentially “closing the loop”.
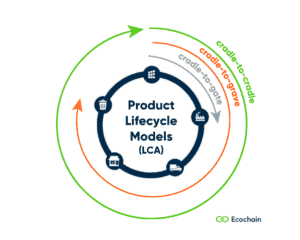
Cradle-to-grave is the standard lifecycle model in our current “linear” (as opposed to circular) economy. We make, use, and discard. However, in the cradle-to-cradle model, we make, use, and reuse.
By using waste products as input for new products, ideally, the Waste Disposal stage in a product’s lifecycle is eliminated. Thus, the Waste Disposal turns into Raw Material Extraction. Waste becomes new resources!
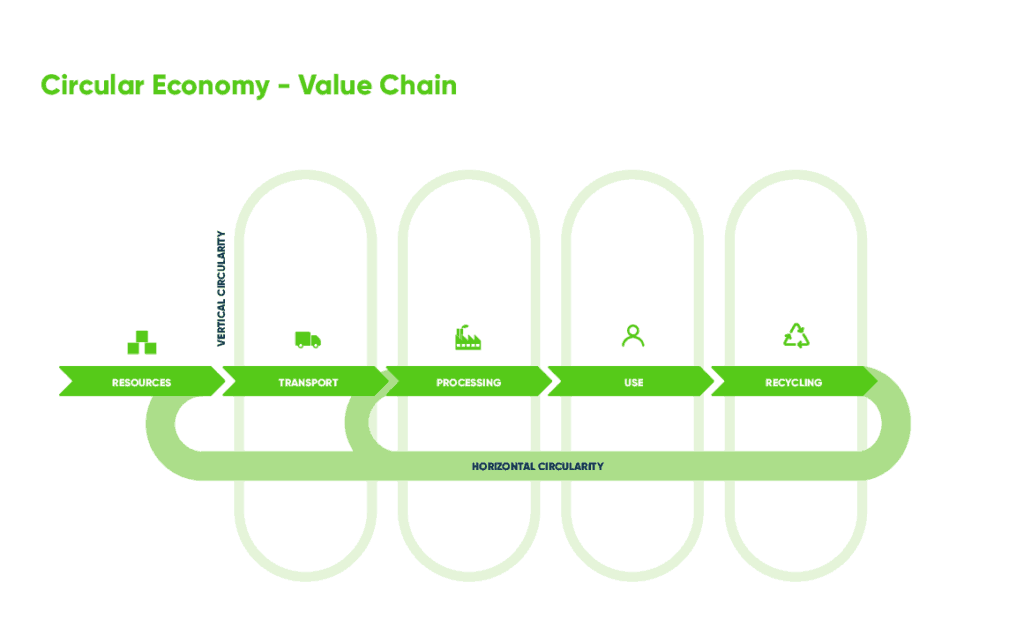
Cradle-to-cradle in product design
In practice, turning Waste Disposal into Raw Material Extraction can be categorized into two levels: reusing (incl. upcycling) and recycling.
Reusing on a component or product level
Many products reach the end of their life because one or two components/materials fail. The other components are still good-as-new. Instead of discarding them, put them to good use:
- Reuse the whole components in a new product (*Upcycling is the same process of reusing old materials. But instead of ‘just’ reusing a material – it’s used to create a product component that’s more valuable or of a higher quality than its original form.)
- Reuse sub-components to make “new” components
- Reuse the broken components after repairing them
To make this possible, design your products in a modular way, with the goal of easy component reuse in mind.
You can also reuse the whole product according to these two ways:
- Upcycling: you reuse the whole product or materials to create a product with a higher quality or value. Some examples of businesses applying upcycling.
- Refurbishing: reuse the whole product by replacing broken components -then sell the product again.
A role model in refurbishing is Ecochain customer Flex IT. They refurbish laptops in an official partnership with HP, ensuring quality through shared production facilities. Through this partnership, they created the first circular IT product line, called: HP Approved Selection. Furthermore, by leasing and renting their products instead of selling them, the responsibility for keeping the products in the economic loop remains with them. It’s a business model in the spirit of the circular economy.
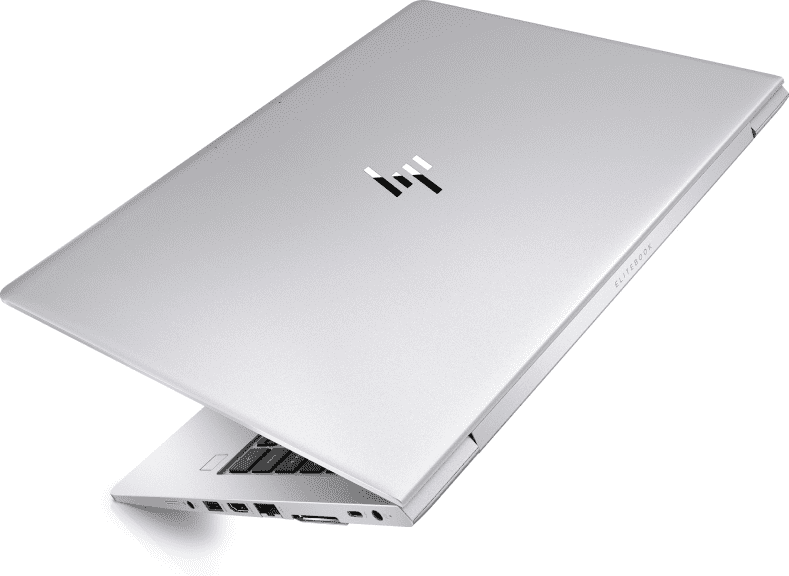
Recycling at the resource level
Recycling means transforming components back into their raw material, to be used again. In case you cannot reuse or repair components, you can recycle the materials. Sometimes 100% of the material can be recovered without quality losses, think of steel.
Unfortunately, many materials lose quality when recycled. This is called downcycling, and isn’t what we want in a circular economy – it gradually kicks the materials out of the economic loop. Therefore, aim to choose to reuse over recycling where you can!
TIPS – When designing components for recyclability:
- Make it easy to separate components into their foundational materials. (Often makes the recycling processes less impactful)
- Keep materials pure. The fewer resource types you mix up, the better they can be recycled.
- Make components that are bound to break – from 100% recyclable materials.
Cradle-to-cradle benefits in LCA
When you design products for cradle-to-cradle, LCA proves the resulting impact reductions in your product’s footprint. But how does cradle-to-cradle exactly change your LCA results?
1. Fewer impacts from reused & recycled components/materials
Using reused and recycled materials can reduce the impact of your product. There are two common methods to calculate this in an LCA:
Cut-off method
Recycled materials have little raw material impact contribution– they didn’t have to be produced from virgin materials after all. However, there are of course accompanying recycling processes that do have an impact.
Reused (and Upcycled) materials have zero impact contribution, as they are reused in their current state – and not broken down like in recycling. Big benefits for your LCA results! However, also in upcycling, you do have an environmental impact associated with the upcycling processes (using the materials in creating a ‘new’ product).
However, recycling and end-of-second-life waste-treatment processes (when the recycled or upcycled material is wasted after its second life) can have significant impacts that do count toward your ‘secondary’ product.
This is called the “cut-off method”. A special version of it is defined in EN15804, which is the basis for environmental product declarations.
50:50 approach
Recycled materials have a fraction of the material’s lifecycle impacts. The size of the impact fraction depends on how many times the material is recycled: if that’s 2, the fraction is ½, if it’s three, the fraction is ⅓, and so forth.
This method is called “50:50 approach” and is used in the EU’s product environmental footprint (PEF). The PEF (an EU-standardized LCA methodology for certain product types) may additionally require correction factors for material quality losses between uses.
Cut-off method vs 50:50 approach
In comparison, the cut-off method results in more beneficial environmental footprints for products that consist of recycled or reused materials. The 50:50 approach distributes the benefits equally between re-uses – which is great when you produce both virgin and recycled materials.
2. Reduced impacts over extended product lifetime
By refurbishing or repairing your products, you extend their lifetime. With increased lifetime, the impact per lifetime decreases.* Environmental claims can then be made with ‘per-lifetime’ metrics. For example: “This product has x % fewer impacts per year of use than comparable products”.
Overall product impact increases here, as replacement components add impacts. Therefore avoid reporting total impacts (“Producing this product has x impacts”). In the bigger picture, the impact reductions are very much there, but that’s because fewer new products get produced thanks to the repair.
However, keep in mind you often have to follow specific Product Category Rules (PCR) to prove this impact reduction.
* This is simple math: environmental scores with the format “impact/lifetime” decrease, as the divisor (lifetime) increases.
Conclusion: always measure
Whether you implement recycling, refurbishing, or repairs in your products’ design – measuring your product’s footprint is essential. Both to know where you’re coming from and to know if your improvements actually make a difference. Start implementing the right to repair in your product – make LCAs.
Measuring Life Cycle Assessments (LCA) was never this easy. With Mobius.
MORE ABOUT MOBIUS