Turning waste into valuable resources
Founded in 1974, Moxba-Metrex is a global specialist in recycling used catalysts* and material residues that contain metals- into new secondary materials.
* A catalyst is a substance that speeds up chemical reactions. Examples of catalysts are; Molybdenum, Nickel, Cobalt, Platinum, etc.
How does Moxba-Metrex’s recycling work?
1. They collect the waste materials from users. E.g. mainly used catalysts from oil refineries or chemical plants;
2. They process these spent materials. E.g. via thermal treatment or melting. This process mostly results in the metals Molybdenum & Nickel- the main ingredients for stainless steel;
3. They produce new secondary materials. The processed metals are used in the production of secondary materials. These materials are often a mix of metals- also called ‘alloy’ materials.
4. They offer secondary materials to manufacturers that mix metals. Their main customers are in the stainless steel industry.
Now- generally these used materials are seen as waste. But, as many metals are completely recyclable, these ‘waste streams’ are actually incredibly valuable material sources.
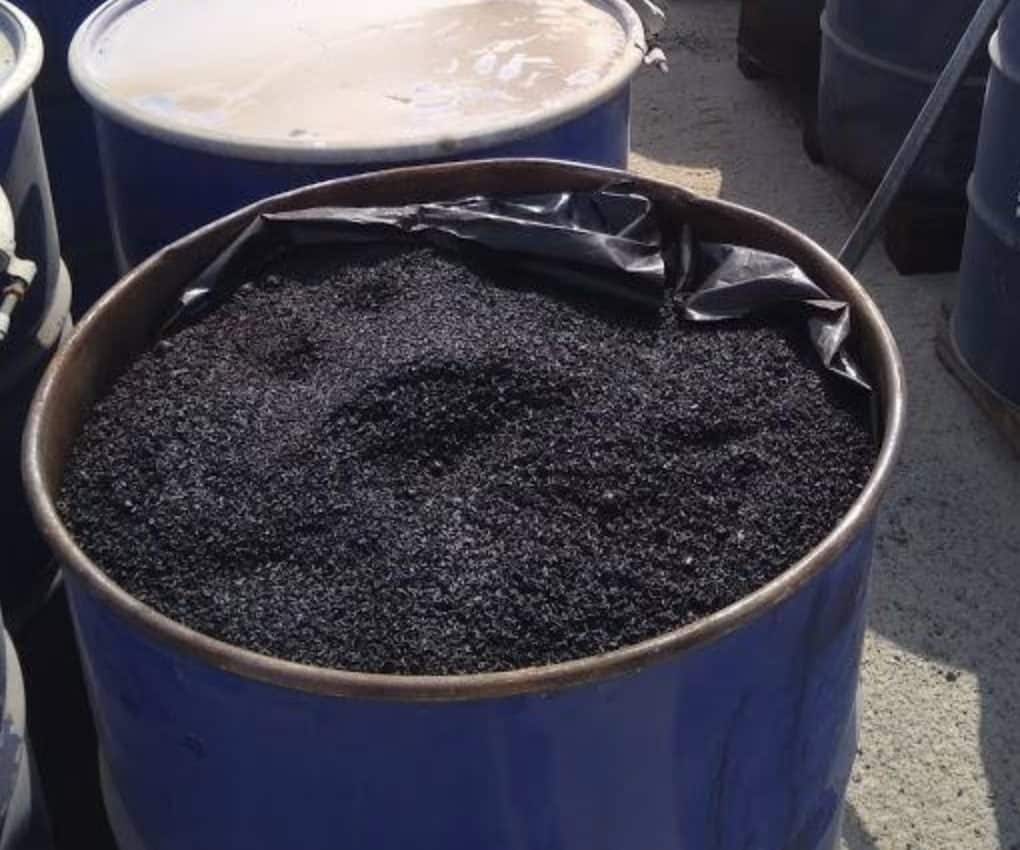
Recycle-hesitation in the metal market
Still, Moxba-Metrex noticed a barrier among their customers in the use of secondary materials: How much more sustainable is it? Does it deliver the same quality? And is it cost-effective?
To answer these questions- they wanted to calculate the environmental impact difference between secondary & primary materials. And proof secondary is the best choice.
So, they reached out to Ecochain.
“We sense a barrier from our customers to use recycled materials. We want to calculate the environmental footprint of secondary materials compared to primary ones. And use these results as one of the main arguments to convince the industry to go ‘secondary’ instead of ‘primary’. We highly believe it has such a smaller impact on our environment.”
Lex van der Sommen, Controller at Moxba-Metrex
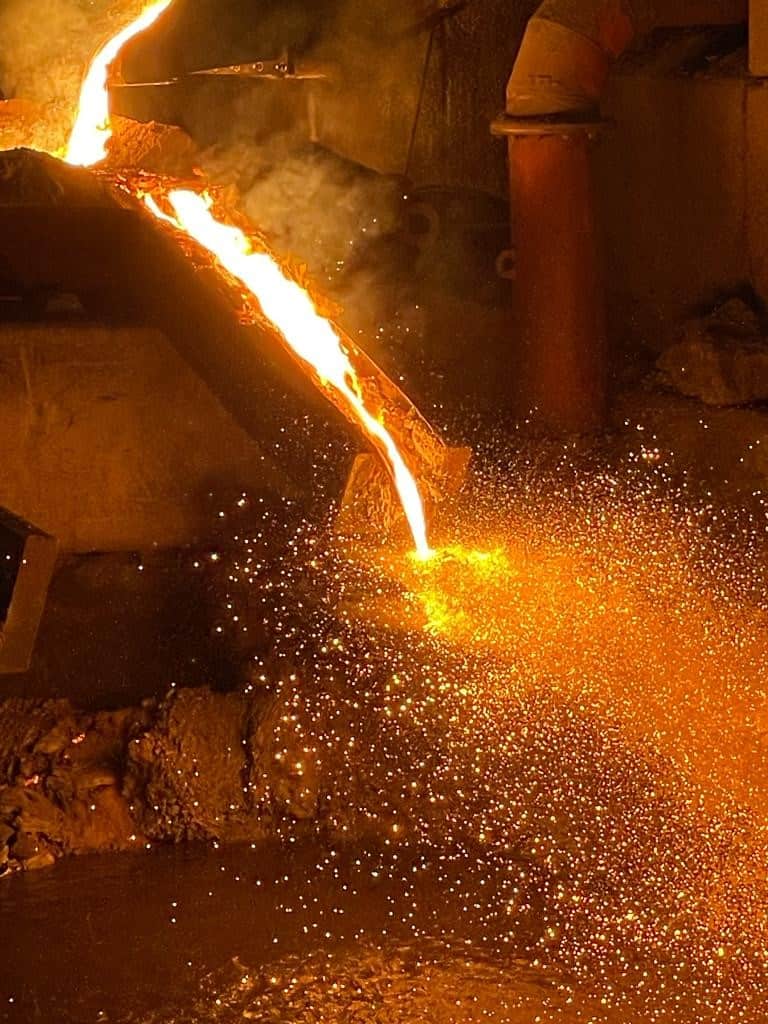
Methodology: What, why & how
Moxba-Metrex’s bestselling secondary material is FeMoNi. FeMoNi is a blend of 3 metals (Iron, Molybdenum & Nickel) and is what makes stainless steel durable and strong. The waste materials Moxba-Metrex recycles for producing FeMoNi, come from the (petro)chemical industry.
To prove secondary FeMoNi is the real deal. Moxba-Metrex wanted to calculate two environmental footprints and compare their impact.
- One footprint of secondary FeMoNi- made from recycled resources.
- One footprint of primary FeMoNi- made from primary resources.
The two footprints were calculated via the method Life Cycle Assessment (LCA). All the product’s stages (recycling process, production of new materials, transport to manufacturers) were included in the calculation. The LCA’s were conducted in Ecochain Helix, revealing 15+ impact outcomes. For simplicity, we focus on the outcome ‘Global Warming Potential’, also known as the carbon footprint.
“The polluter pays principle”
Moxba-Metrex recycles waste products and turns them into new ones. This means they are not responsible for the environmental impact from the production- until the waste phase of the used products they take in. Only for their own processes.
Moxba-Metrex’s environmental footprint calculation starts from the moment the waste materials come into their recycling plants. Everything before that belongs to the producer of the waste.
“We wanted to specify the environmental impact of our products compared to the primary equivalents. Additionally, we want to see where we can improve our own processes.”
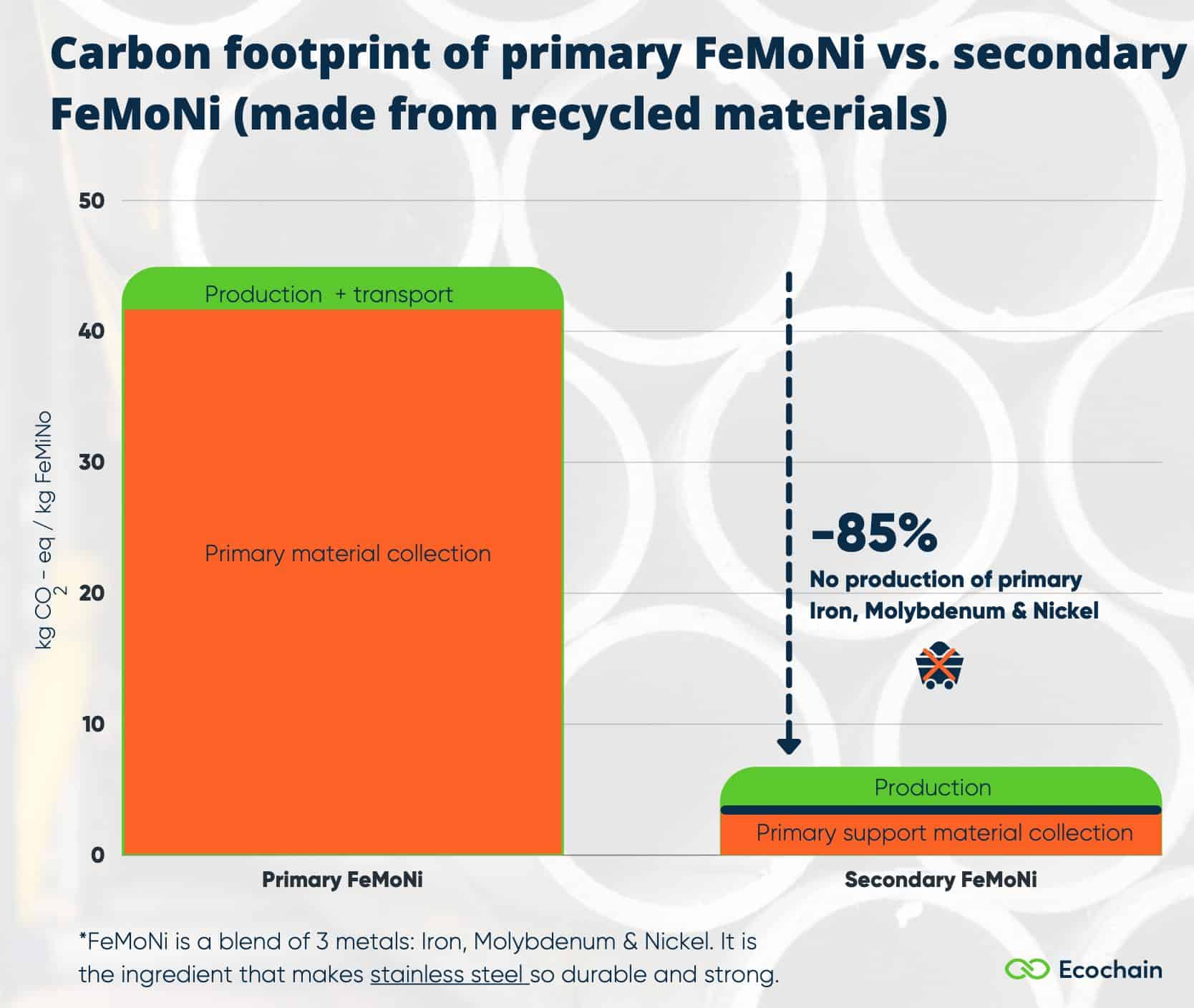
Secondary FeMoNi has 85% less impact than its primary counterpart
Secondary FeMoNi beats primary FeMoNi without a doubt.
With a carbon footprint of 6,72 kg CO₂-eq compared to primary FeMoNi’s 44,9 kgCO₂-eq, the difference is a staggering 85%.
The main impact difference between the two materials lies in retrieving (mining) the primary materials for producing primary FeMoNi. This phase accounts for almost the entire environmental footprint of primary FeMoNi (image 2) and only for 41% of secondary FeMoNi.
The main takeaway: Recycling metals into secondary materials- simply avoids the production of primary ones.
What are the impact hotspots for secondary FeMoNi?
The results also show the biggest impact hotspots (image 3) of secondary FeMoNi:
1. Production phase: With 45%, the main environmental impact hotspot for the secondary FeMoNi comes from its production processes. Big contributors here are the use of ovens. (You need a lot of heat to melt and mix metals)
2. Material collection phase: With 41%- the second-largest impact hotspot comes from collecting the primary materials necessary for the production of the secondary FeMoNi.
3. Transportation phase: With 14%- the third-largest impact hotspot comes from transporting the processed materials to the production site of the secondary FeMoNi– in Brazil. Think of transport via shipping and trucks.
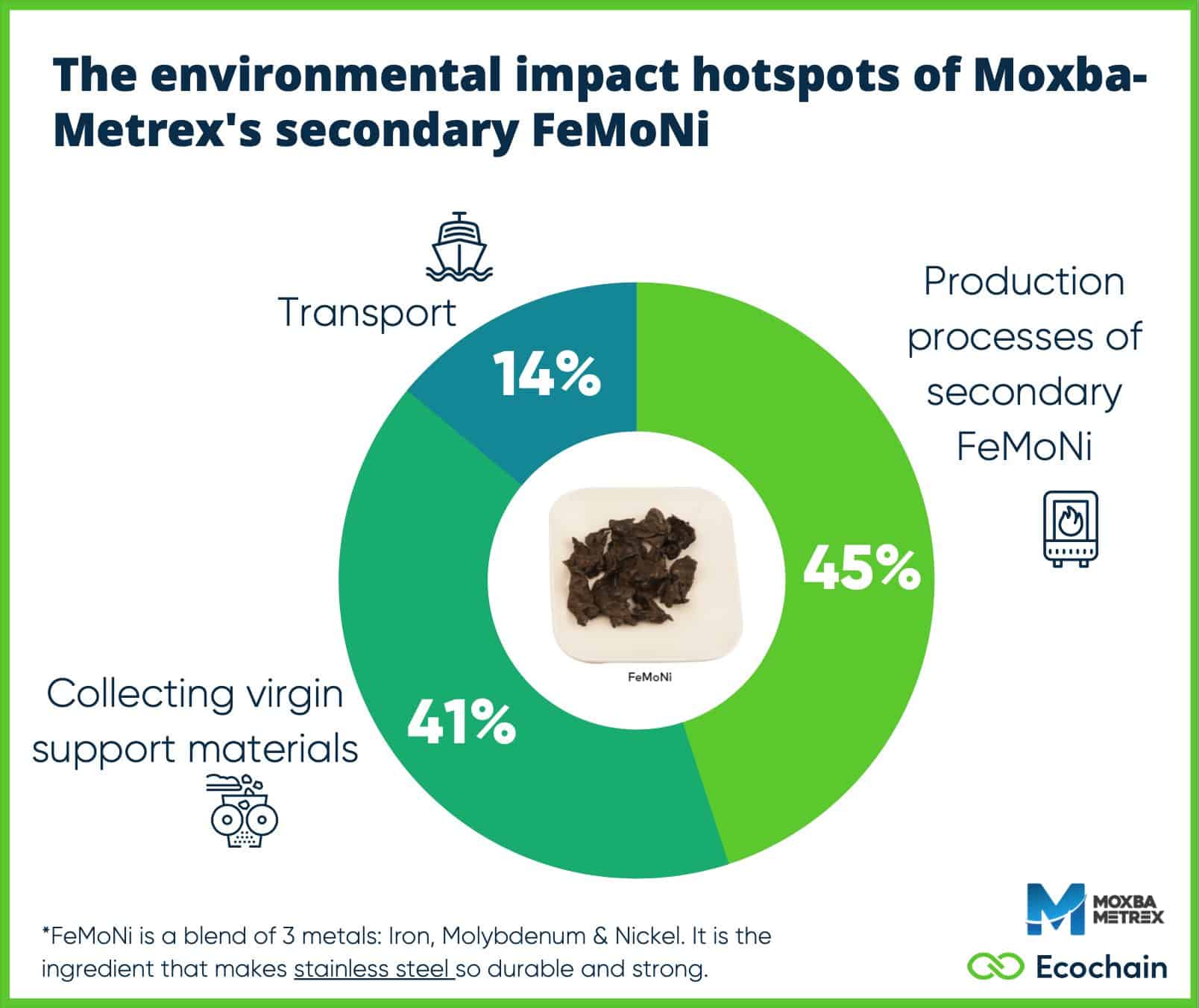
Secondary materials are also more cost-effective
The LCA highlights the benefits of Moxba-Metrex’s recycling process compared to the traditional mining of metals.
Secondary FeMoNi allows customers to lower their own footprint. But it’s also cost-effective:
- Moxba-Metrex buys waste– not expensive primary materials.
- Secondary FeMoNi has a lower melting point than the usually used material for stainless steel; FeMo. This means FeMoNi melts into steel faster. Shortening the production process of stainless steel, and making it more cost-effective.
- They use the heat from burning waste materials (especially released oil) to constantly heat their own ovens. Only needing new oil and gas to start up the ovens.
Even recycling processes can improve
The impact hotspots from the LCA also show Moxba-Metrex where to improve:
A large part of their impact comes from the primary supporting resources (41%) they need to produce the secondary FeMoNi. Therefore, Moxba-Metrext will recycle these materials and buy secondary resources as much as possible.
Secondary materials: a KEY step to creating a circular economy
Comparing these two materials shows the value of recycling:
- It takes out the often most impact-heavy phase in a product’s lifecycle: producing new raw materials/ingredients.
- And replaces it with endlessly availabe resource streams = it’s the key pre-condition in transitioning towards a circular economy.
Especially in a conservative market such as iron and steel- secondary materials can put a stop to the endless depletion of the planet. It’s simply unnecessary to use primary materials when secondary materials have the same quality- minus the impact.
Endless streams of high-demanded resources, without immensely depleting the earth? Sounds like a win-win for every company.